An Overview of Glass Batch Lamination Using Vacuum Batch Lamination Oven
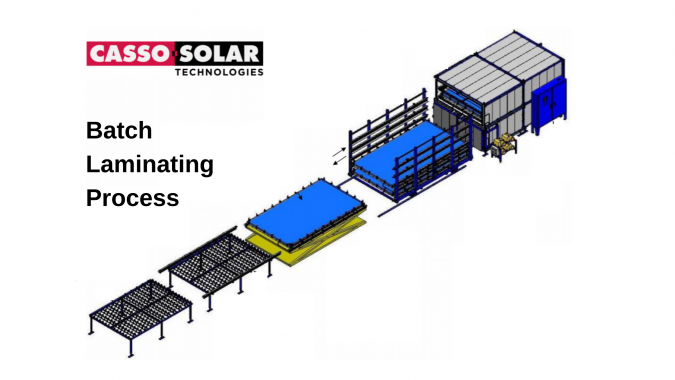
Introduction
Laminated glass is used in various structural and architectural applications to provide additional durability, versatility, and strength when compared to monolithic glass.
Laminated glass is constructed of two or more sheets of glass, which are held together using an interlayer material such as polyvinyl butyral (PVB) or ethylene vinyl acetate (EVA).
The interlayer material bonds to the glass sheets forming a strong multi-layer structure. This post focuses on one of the methods for creating laminated glass, which in all cases is done with a combination of heat and pressure.
Here, we are exclusively focused on the vacuum bag lamination process using the batch lamination oven designed by Casso-Solar Technologies.
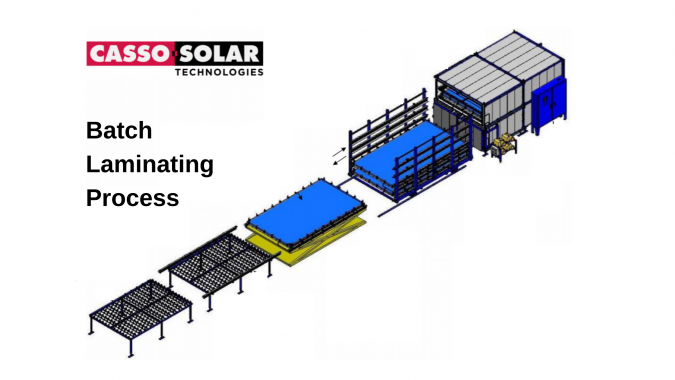
Steps Involved in Glass Batch Lamination Using Non-autoclave Vacuum Bag Lamination Oven by Casso-Solar Technologies
Let’s understand the different parts of the Casso-Solar Technologies batch lamination system and how they work in the vacuum bag lamination process.
- Caster Table – Clean glass exits a washer and is staged on the caster table while awaiting assembly
- Layup Table – On the layup table, two (or more) sheets of glass are assembled on top of one another with interlayer material in between. The glass sheets are aligned and the excess interlayer is trimmed around the edges. Most glass manufacturers then tape the edges of the assembly using special breathable tape to hold it together throughout the process.
- Part Carrier – Completed assemblies are transferred to one of the parts carriers which consist of a wheeled frame that holds a silicone vacuum bag. The parts carrier has wheels to allow it to easily transfer between the different equipment components. The vacuum bag has an interlocking seal around the edge to form an air-tight environment.
- Transfer Deck & Hydraulic Lift – The parts carrier is wheeled onto the hydraulic lift which raises or lowers to position the carrier in line with one of the racks on the transfer deck. Each transfer deck rack is aligned with a corresponding rack in the oven. Carriers remain on the transfer deck until it is time for processing in the oven.
- Laminating Oven – The oven is where the actual lamination happens. Using vacuum pumps to pressurize the vacuum bags and a combination of infrared and convection to apply the heat, the oven runs a PLC-controlled processing cycle to laminate the parts.
Now it is important to understand what is happening during the lamination cycle in the oven, as knowledge of the process is crucial in successful operation of any lamination equipment. The lamination process has (4) main phases: Pre-Vacuum, Melting, Cross-Linking/Curing, and Cooling
- Pre-Vacuum Phase – In this phase, the vacuum pump(s) is run for 10-15 minutes before the heaters are turned on. This allows the pump(s) to remove all of the air from the vacuum bags, which applies pressure to the assemblies.
- Melting Phase – Once pre-vacuuming is complete, the heaters turn on and bring the oven temperature up to approximately 194°F (90°C). During this phase, the interlayer melts into a liquid state and fills up any voids between the sheets of glass. The vacuum pump continues to run to remove any trapped air from between the glass sheets to ensure no bubbles remain at the end of the process.
- Cross-Linking/Curing Phase – After melting, the oven temperature is further increased typically somewhere between 230-266°F (110-130°C). At these temperatures the interlayer goes through a change called cross-linking which bonds it to the glass. Generally speaking, the higher the curing phase temperature, the shorter time required to properly cross-link the material. The vacuum pump typically remains on during this stage as well to promote bonding by applying pressure to the assembly.
- Cooling Phase – Once curing is completed, the assembly is cooled down. For most interlayer materials it is common for this stage to be completed as quickly as possible. Faster cooling typically leads to higher clarity in the final appearance of the parts. Once the assembly is below the melting temperature, the vacuum pump can be shut off.
It is important to note that while the phases listed above are the same for all interlayer products, the temperatures given are a general guideline.
Each interlayer material and manufacturer has different recommended times and temperatures for each of the phases and the manufacturer guidelines should be consulted when setting up a lamination cycle recipe.
For example, PVB has a higher moisture content than EVA and takes over 30% longer to process as a result.
This vacuum bag lamination process can be employed to produce many types of products including annealed laminated glass, appliance glass, laminated bent glass, and tempered laminated glass.
In addition to this lamination oven system, Casso-Solar Technologies also provides various types of glass processing equipment such as spandrel drying ovens, dryers for digital and screen print inks, nip roller lamination lines, SentryGlas Trim table, glass bending systems, rolling hearth furnaces, and glass casting furnaces. Our team can help specify the appropriate equipment for your application, please give us a call at (845) 354-2010 to discuss your needs.