Short vs. Medium Wave IR Heating: Which One Is Right for Your Manufacturing Process?
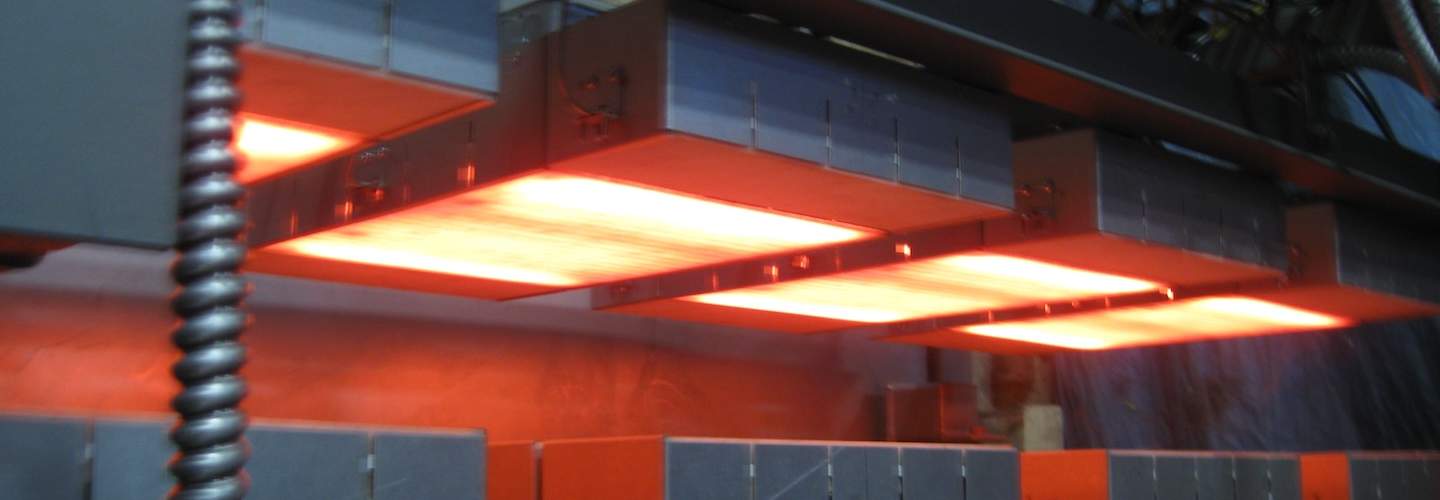
How to Select the Optimal Infrared Wavelength for Heat Processing in Manufacturing
Manufacturing cycles often require heat to process materials and produce finished goods. Many manufacturers turn to infrared (IR) heating processes to provide energy efficient, high-intensity heat for various drying applications. More than 60 years ago, Casso-Solar Technologies started out as a simple infrared heaters manufacturer. Since then, we’ve continually developed our products to meet the complex, custom specifications of our clients’ projects.
Our IR heating solutions fall under two main types of infrared heat:
- Short-Wave Infrared Heating: Wavelengths are between 0.76 and 2 microns
- Medium-Wave Infrared Heating: Wavelengths are between 2 and 4 microns
Learn more about how infrared heating works, the differences between short-wave and medium-wave infrared heaters, and their respective pros and cons.
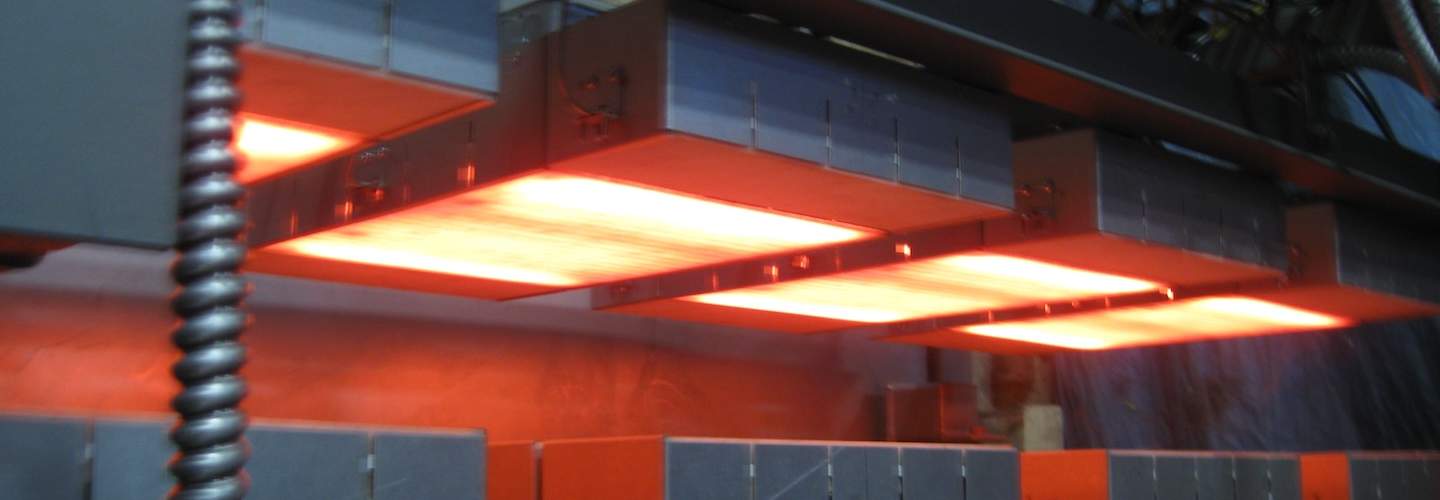
How Does Infrared Heating Work?
Infrared heating is a reliable, basic heating method that integrates well with a myriad of manufacturing processes. The infrared energy wavelength of an object depends on its temperature. The higher the temperature an object produces, the shorter its energy wavelength, resulting in a higher output of energy. Infrared radiation is electromagnetic energy that is categorized as short-wave,medium-wave, and long-wave infrared, with short wavelengths providing the highest energy output and long wavelengths having the lowest. Long-wave or beyond longwave infrared can be too inefficient for industrial heating processes, so they generally are not used.
Manufacturers must consider both the efficiency of the infrared heat itself and the heat absorption factor of the material being processed. As a more intense heat source than convection heat, infrared heat should be applied directly to your process materials in an industrial infrared oven. These electric ovens help control the timing and amount of heat applied to avoid product damage or overheating. Consult our infrared heating specialists to determine the best way to apply infrared heat to your project.
Benefits of Electric Infrared Heating From Casso-Solar
Our engineering team has developed a wide range of heaters, each one consistent with the temperature needs of different manufacturing processes.
Some of the key benefits of an electric infrared heating solution from Casso-Solar Technologies include:
Accurate Process Control:
Our IR heaters provide consistent temperatures that can be controlled and monitored easily by operators. Each heater can be programmed with customer-specific recipes, and we can upgrade or alter the controls upon request.
Uniform Heating:
If you need uniform heating throughout your materials, we provide flat panel infrared heaters featuring heating elements bonded to refractory that can handle high heat.
Design Flexibility:
Choose from our standard selection of infrared heaters or speak to our development team about custom options.
Durability:
Casso-Solar only uses high-quality components in our electric IR heaters, meaning that they require little to no maintenance throughout their useful life, which lasts tens of thousands of hours.
Energy Efficiency:
Our electric IR heaters are extremely efficient with their power consumption. For instance, our DuoTube heaters feature an integrated ceramic coating reflector to ensure that most of the infrared energy generated is directed at the product.
No Harmful Emissions:
IR heaters provide radiant heat without relying on the ignition or combustion of energy sources that can produce contaminants, toxins, or on-site emissions.
Quartz Heating Elements:
Our quartz heating elements maximize the energy that passes through them, providing very efficient heating. They can be found in our Unitube, DuoTube, and Type C+ heaters.
Short-Wave Infrared Heating (“Near Infrared”)
Short-wave infrared heating systems use short waves, which give off more energy and operate at higher temperatures. As a result, these heaters offer high-intensity heat that can reach 5000°F or higher. Our Casso-Solar SWL Unitube Heater can radiate waves between 0.76 and 2.0 microns, and operators can control the wavelength to align with the peak absorption point of process materials. Each unit includes controllable emitters that can be shut down to preserve energy, modified for temperature profiling, and more.
Advantages and Drawbacks
Short-wave infrared heaters offer a lot of heating power. The shorter wavelengths can increase the amount of energy absorbed by the heated objects, and short-wave heaters can reach higher temperatures than medium-wave heaters. However, the higher operating temperatures of short-wave heaters can lead to shorter equipment lifespans over time.
Applications
Some of the most popular applications for high-temperature short-wave IR heaters include:
- Powder Coating Applications
- Processing Metals: Such as Continuous Coil Coating Lines
- Processes that need short, efficient heat cycles, such as high-volume orders on a tight schedule
Medium-Wave Infrared Heating
Medium-wave infrared heating solutions radiate heat with longer length-waves. Our DuoTube heating unit can reach high temperatures of up to 1400°F or 1750 °F, depending on the coating or refractory selected. The gold-coated DuoTube has a dual-coat integral gold reflective coating, which does not oxidize and can reach temperatures of up to 1400°F. The white refractory DuoTube works on a wider emission spectrum and can reach temperatures of up to 1750°F. Both types are completely maintenance-free throughout their useful life.
Advantages and Drawbacks
Medium-wave IR heaters produce a high level of energy and can last longer than their short-wave counterparts. They are ideal for drying operations and handling water-based coats, as water can easily absorb medium-wave energy. However, these heaters have alower power density than short-wave heaters and thus require a larger footprint to deliver the same amount of energy.
Applications
Some common applications for medium-wave IR heating are:
- Plastic Film Heating for 1mm Thick Sheets
- Drying Water- and Solvent Based Coatings
- Glass Processing: Including Bending, Firing, Laminating, and Drying Inks
- Drying and Heat-Setting Textiles
Comparison of Short-Wave vs. Medium-Wave IR Heating
Both short- and medium-wave IR heating systems can heat manufactured goods for processing and finishing, and each one works best for different contexts. Short-wave IR heaters are extremely energy efficient and can reach higher temperatures; the heat can also quickly penetrate objects based on their peak absorption point. Medium-wave IR heaters produce a lot of energy and tend to have a longer lifespan. Our team can help you select the right heating unit based on your manufacturing processes and needs.
Talk an Infrared Applications Specialist
At Casso-Solar Technologies, we’ve developed infrared heating solutions for over 60 years. We work with each of our clients to ensure they have custom-fitted solutions that integrate with their existing processes and needs, and we partner with each client through the design and implementation process to ensure complete satisfaction. Contact us today to learn more or to get started.